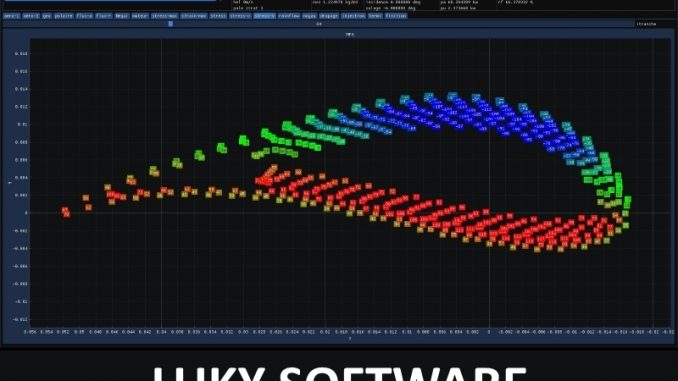
Profiles optimization using Artificial Intelligence
The LUKY software is an aerodynamic, mechanical and manufacturing process model of E-Props propellers, fully developed and enriched since 2007 by Jérémie Buiatti and his team of engineers. It uses the C++ programming language.
LUKY allows to model directly the behavior of a complete E-Props propeller (blades and hub) on a given engine, from an aerodynamic and mechanical point of view, including vibration and fatigue life.
This software is a model of the type lifting line for the speed of execution, in order to allow the exploration of the domain of possible propellers with the help of an evolutionary algorithm (metaheuristic), in order to automate the search for propeller solutions (mechanical and aerodynamic dimensioning) for a given problem, to best meet the user’s specifications.
LUKY is also coupled to an aerodynamic model of the free vortex wake to verify, in extreme cases, the relevance of thelifting line model.
For the mechanical part, a Finite Element Dynamic Beam model with damping is used. It simulates and analyzes the behavior of the blade in bending and torsion, which allows, once coupled with the aerodynamic model, to be representative for the Stall Flutter, for the possible resonances with the engine and for the bird strike. A Rainflow-type algorithm is used to compare the stresses to the fatigue tests, and thus to define the propeller’s lifetime.
The LUKY software allows to model the manufacturing process of the E-Props propellers: drawing of the mold, lamination plan and cutting program of the carbon fabric, machining program of the foam core, dimensional control scan program, machining program, drilling and grinding of the blade root.
When designing new propellers with LUKY, the more information the E-Props team receives about the engine concerned, the more accurate the design will be. If it is a piston engine, the relevant information is the number of pistons, the mass of the piston-rod assembly and the moments of inertia and torsional stiffness of the crankshaf, the compression ratio.
If there is a torque damper device, it is for example its angular deformation-torque response law that will reveal all the vibratory modes likely to be encountered in the use of the propeller, in order to define their impact on the life span and what would be the possible resonances to be checked during the test campaigns.
It also allows to simulate a gearbox design.
More recently, with the arrival of the eVTOL configuration, LUKY integrates the realization of models for a strongly oblique attack, in order to characterize the impact on the propeller and its life and to define the loads to which the engine will be subjected in terms of wave torque. This can go as far as a complete modeling of the engine support arm, engine and propeller assembly to verify the dynamic behavior of this whole assembly in oblique attack and at different operating speeds.
The same code is used to verify the lateral wind loads for aircraft installations.
The LUKY software integrates all the functions of propeller design and manufacturing, which makes this software accurate and competitive in use in order to perform studies of a very high quality for a reasonable cost.
Article dans la revue en ligne ULMAG : Logiciel E-Props Luky
Leave a Reply
You must be logged in to post a comment.